Instant of Change, 17–22 April 2023
The Instant of Change is the moment when design meets art, in a single object, a piece never seen before. Three noble materials: Corian®, porcelain stoneware and stainless steel, come together to create a work that is the result of the creativity of Finemateria design studio. An experience that connects Ceramiche Caesar, QuadroDesign and Rexa in the Mo.1950 Showroom, in Via Molino delle Armi 14 Milan. Opens Mon-Sat from 10AM to 8PM.
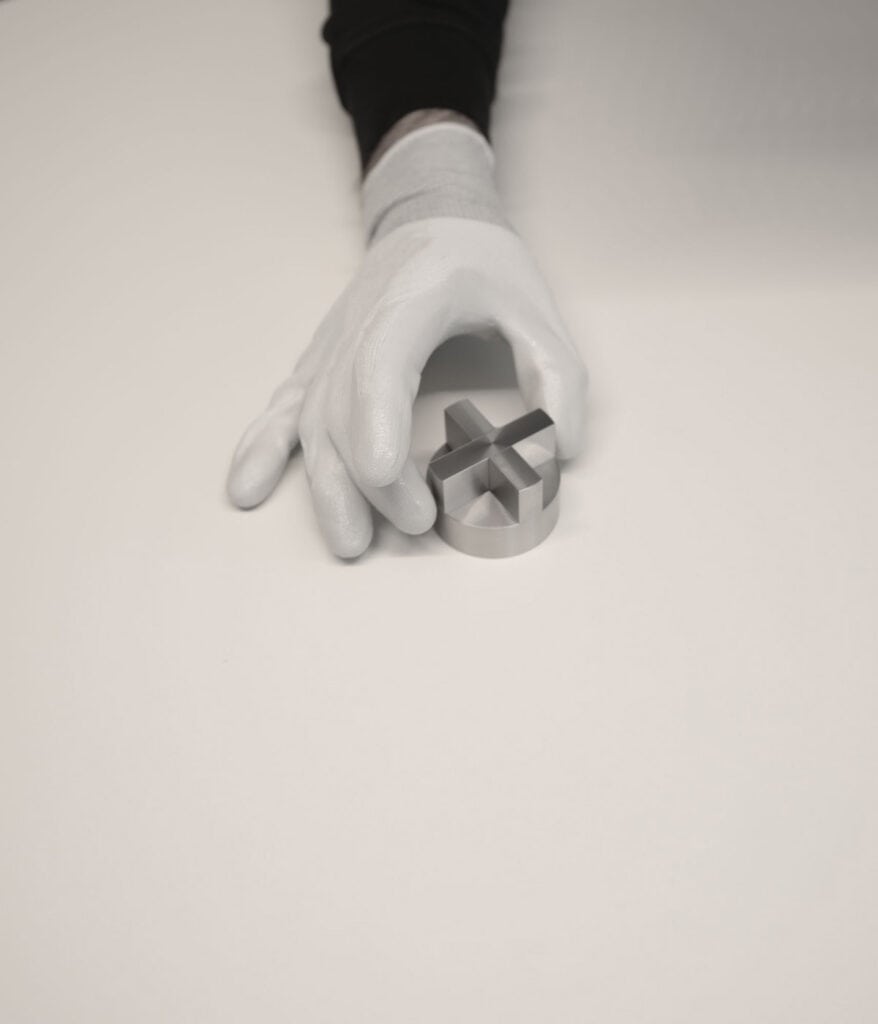
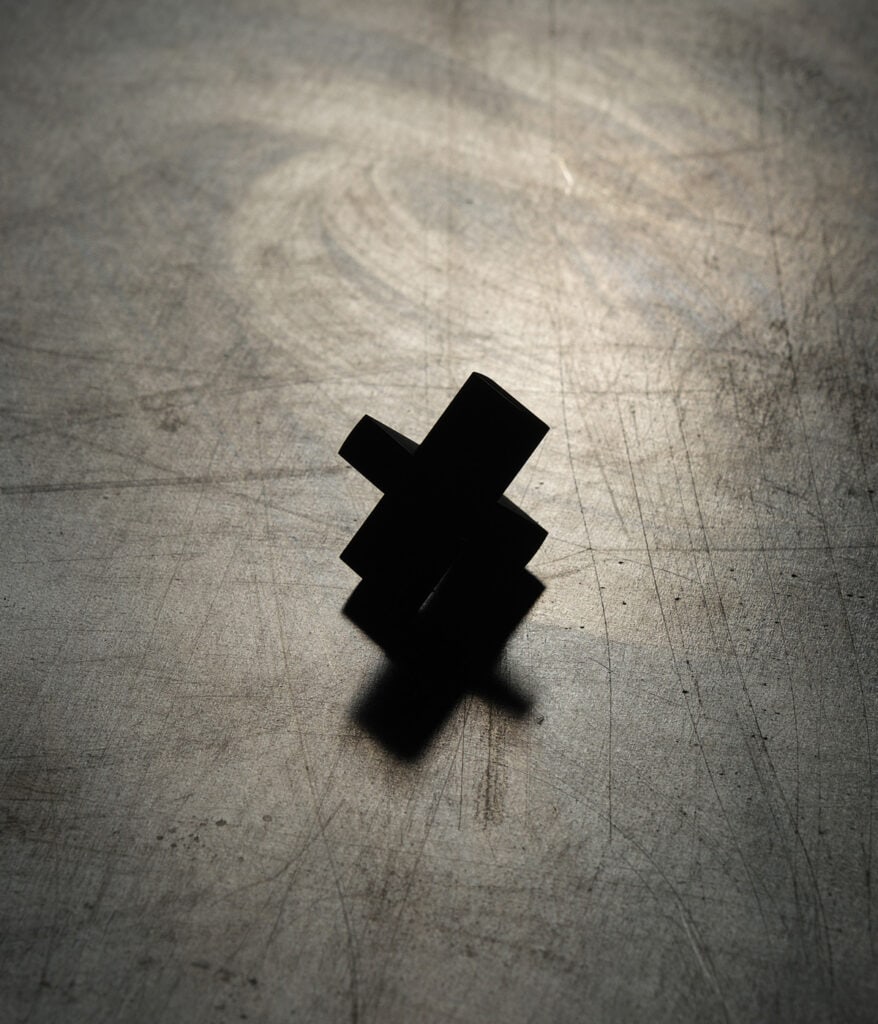
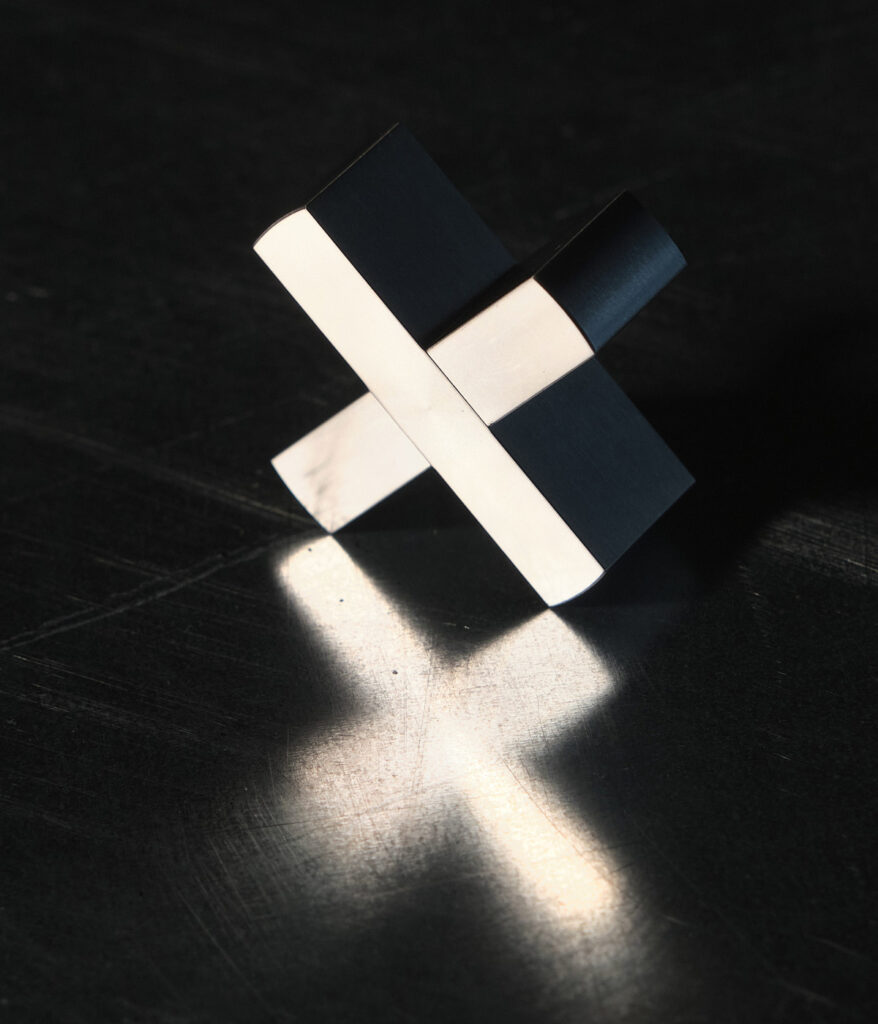
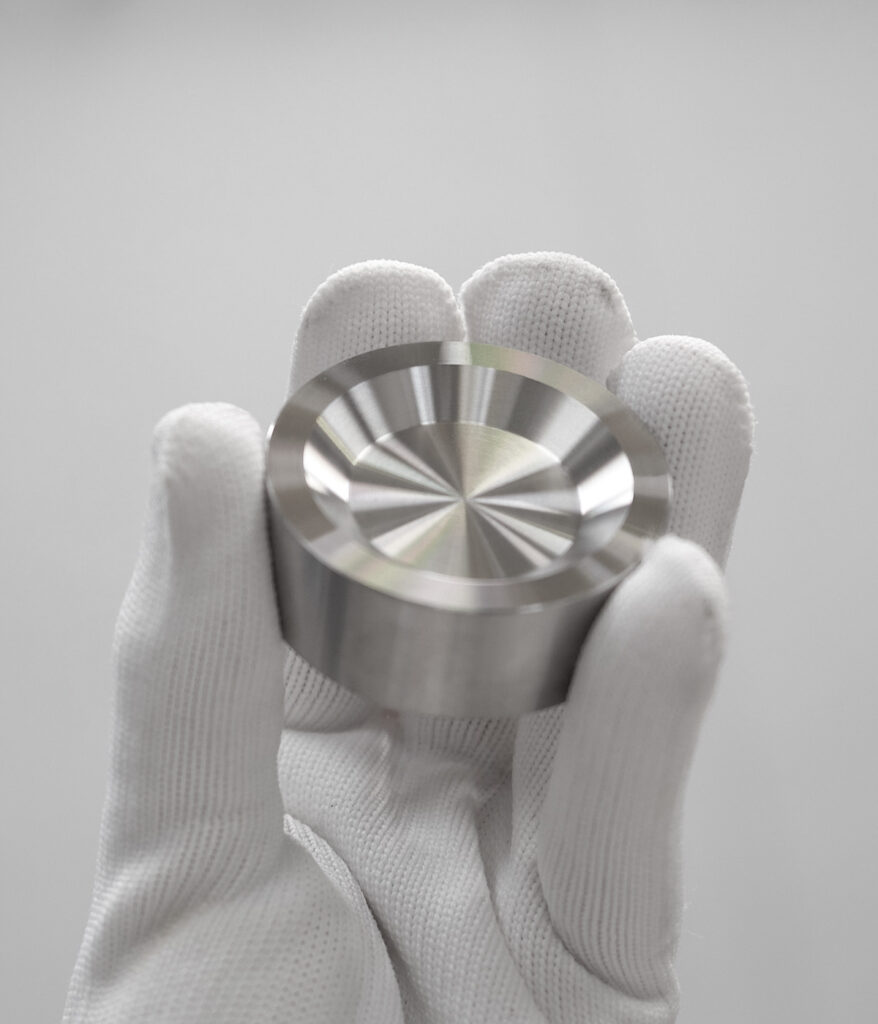

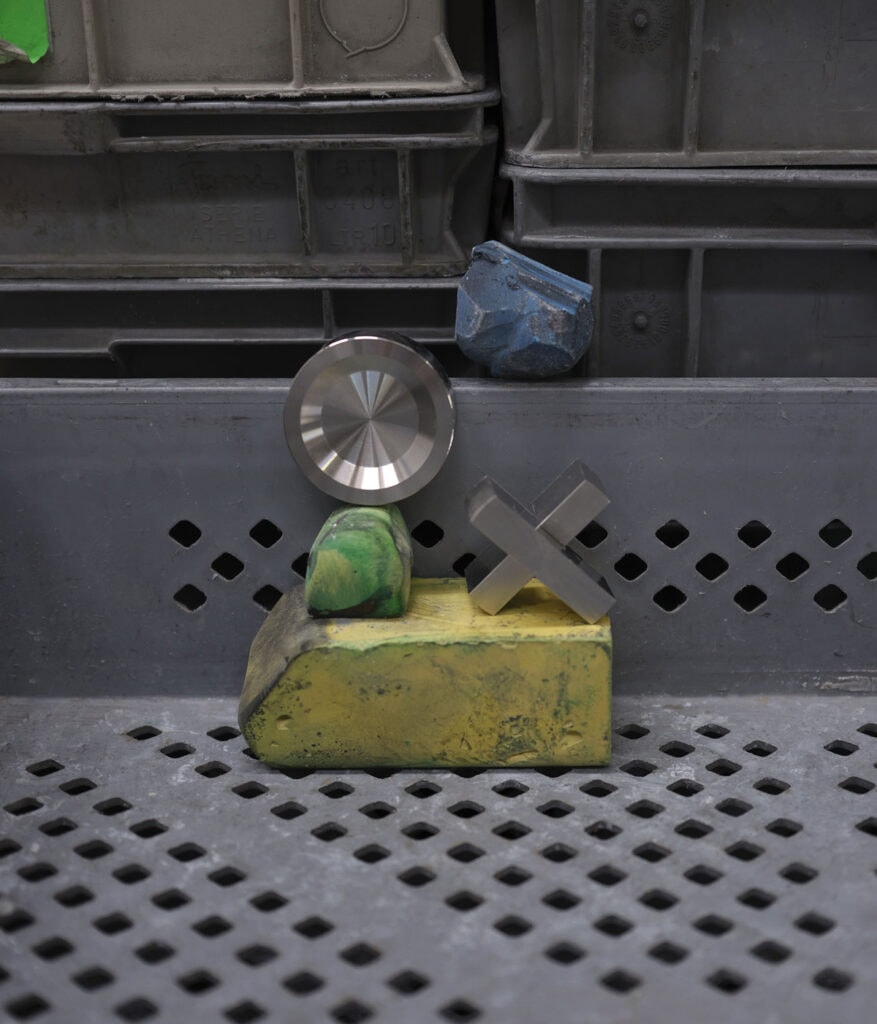

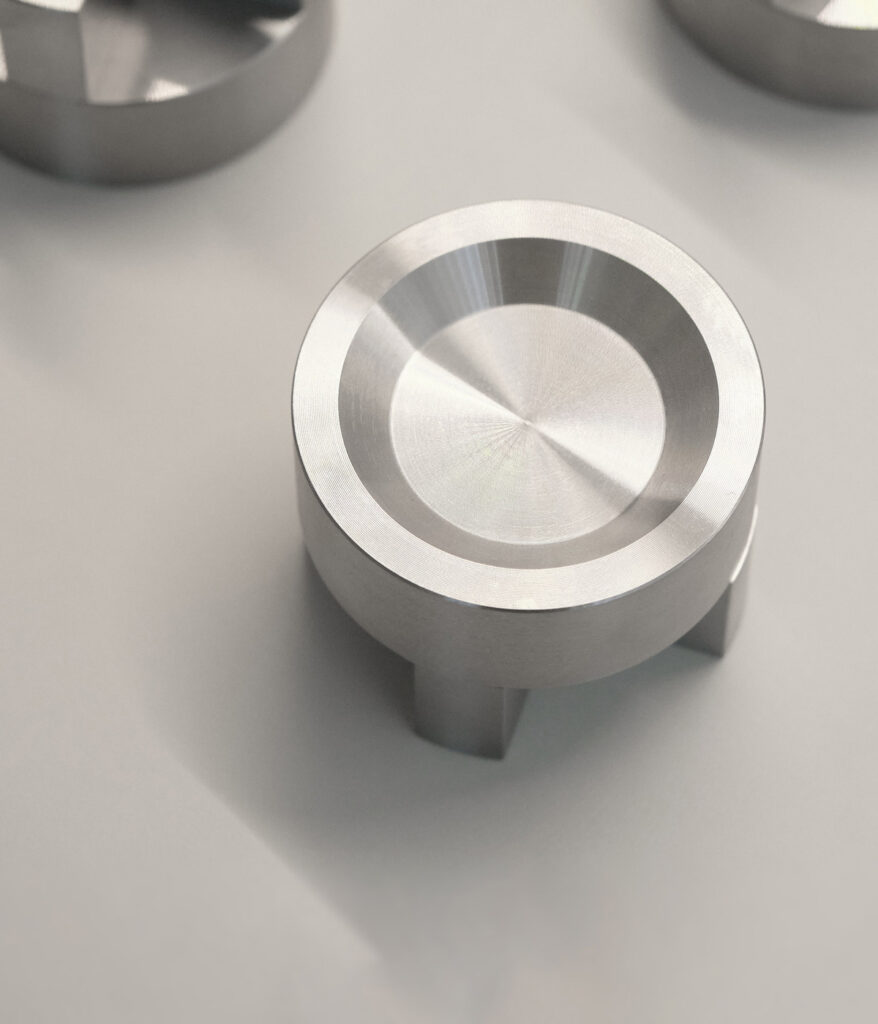
When design meets art, a design idea becomes a volume that can be touched and used. So Finemateria, Italian designers, design and think an object that invites the user to interact with it and with their fellow man: “All materials will touch each other, people will touch them, creating from a sensory and tactile point of view a very deep interaction.” The three materials mutate into a single object merging in skills and abilities, playing together in a repeated series of moves that aggregate, unite and entertain.
1. Tris is an object, a design idea, a unique work.
2. Tris represents three dimensions, the third edition of The Instant of Change, the union of three different materials and three different companies, Ceramiche Caesar, QuadroDesign and Rexa.
3. Tris is both in the game and in the union of people.
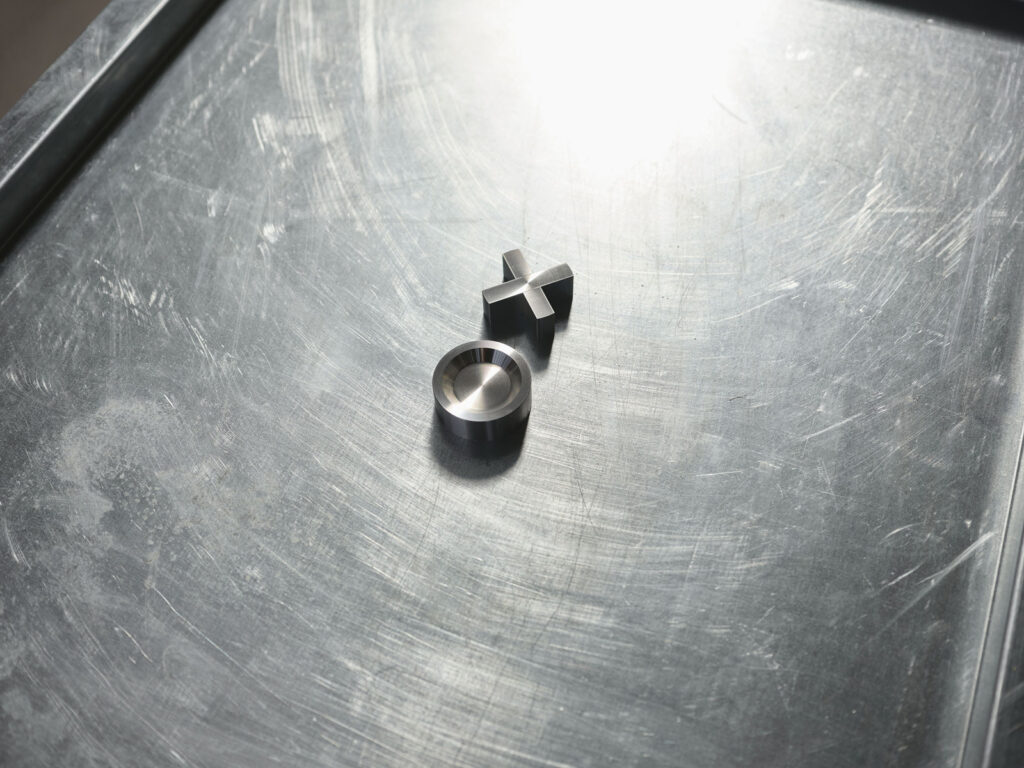
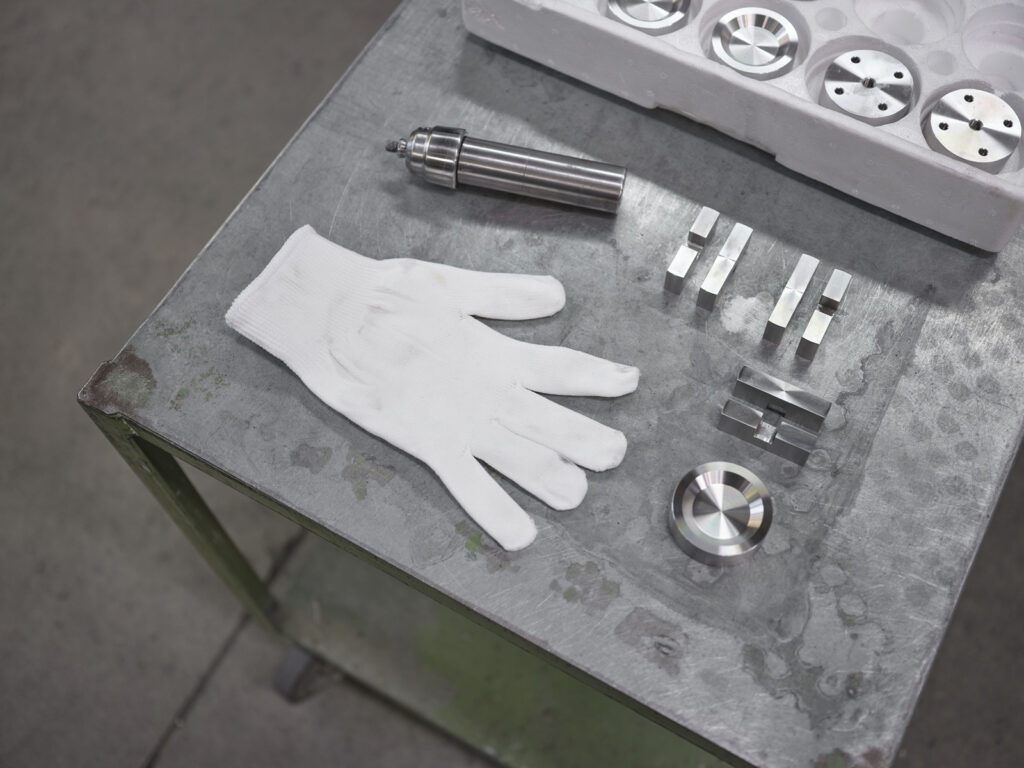

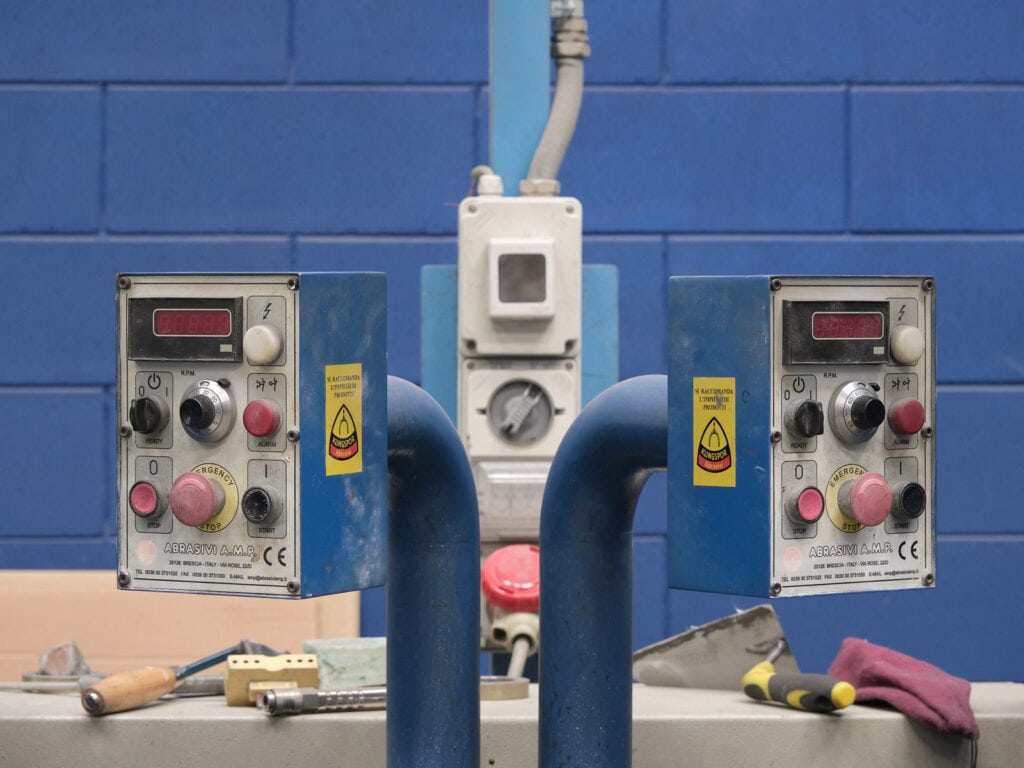
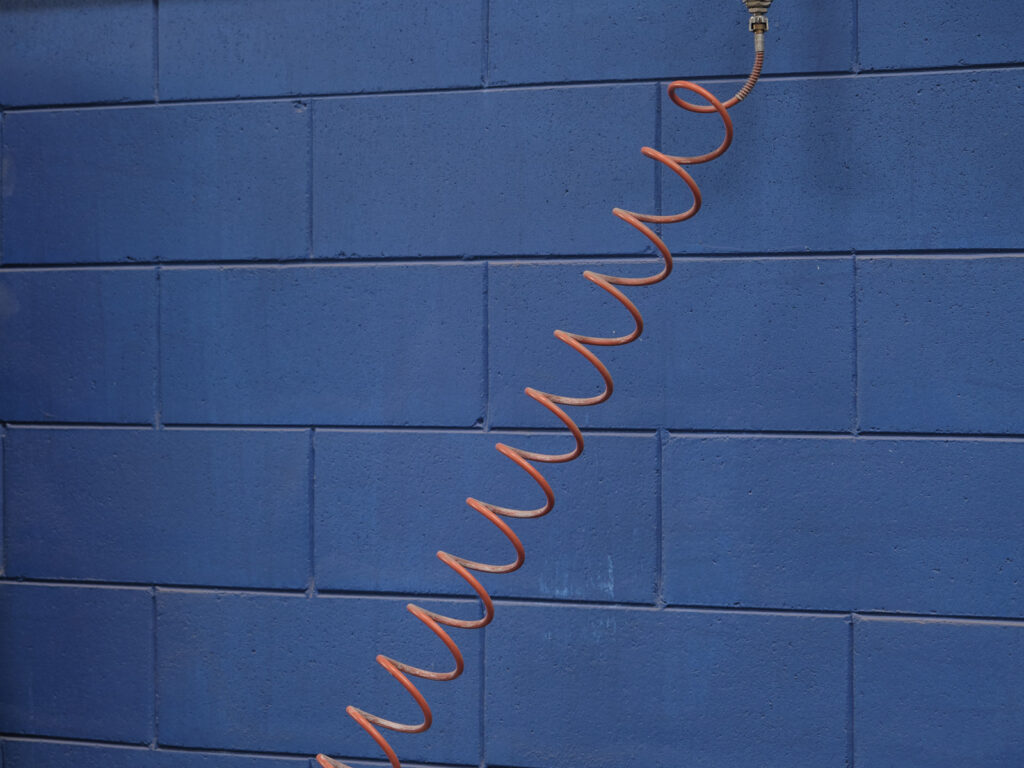
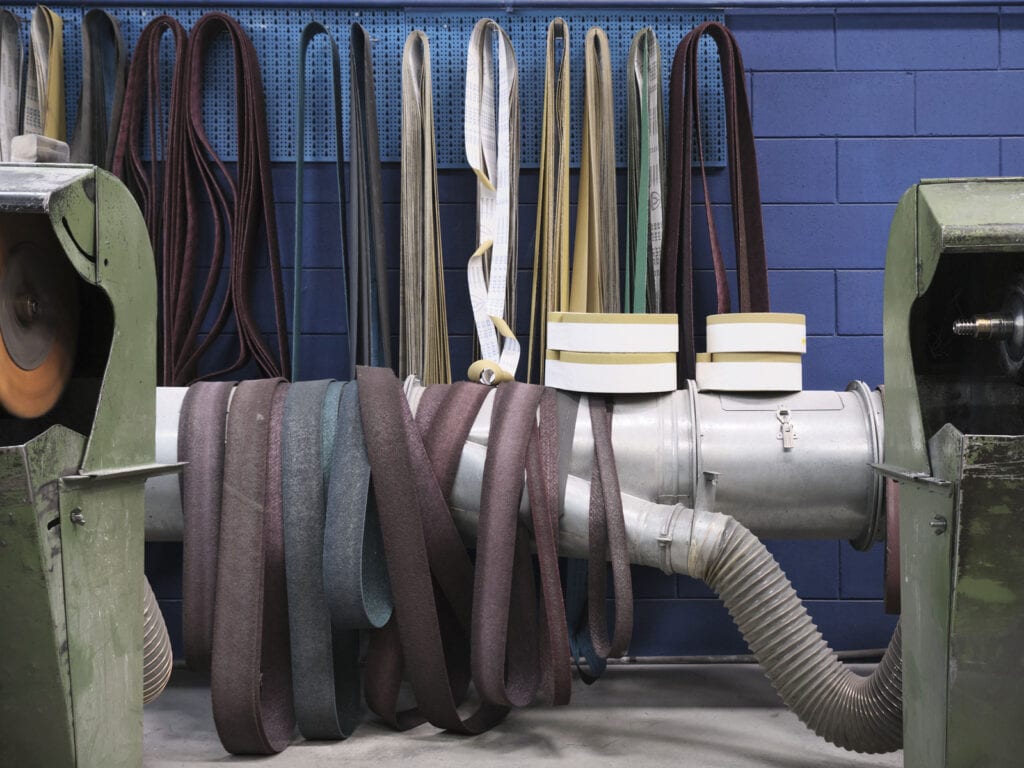
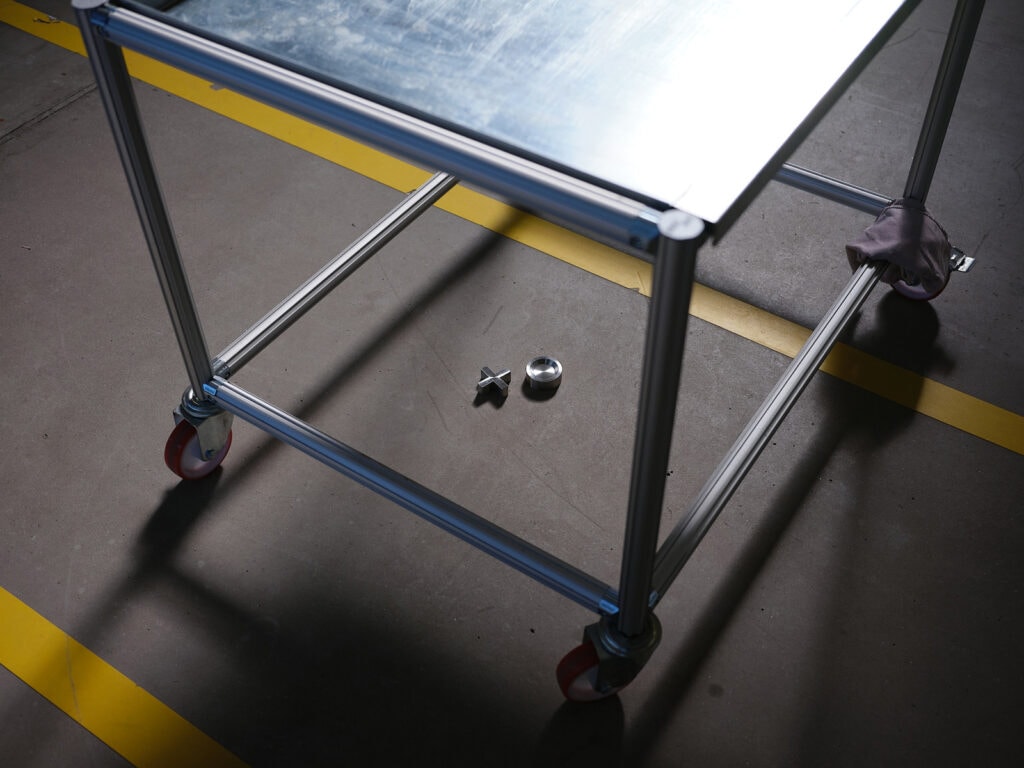
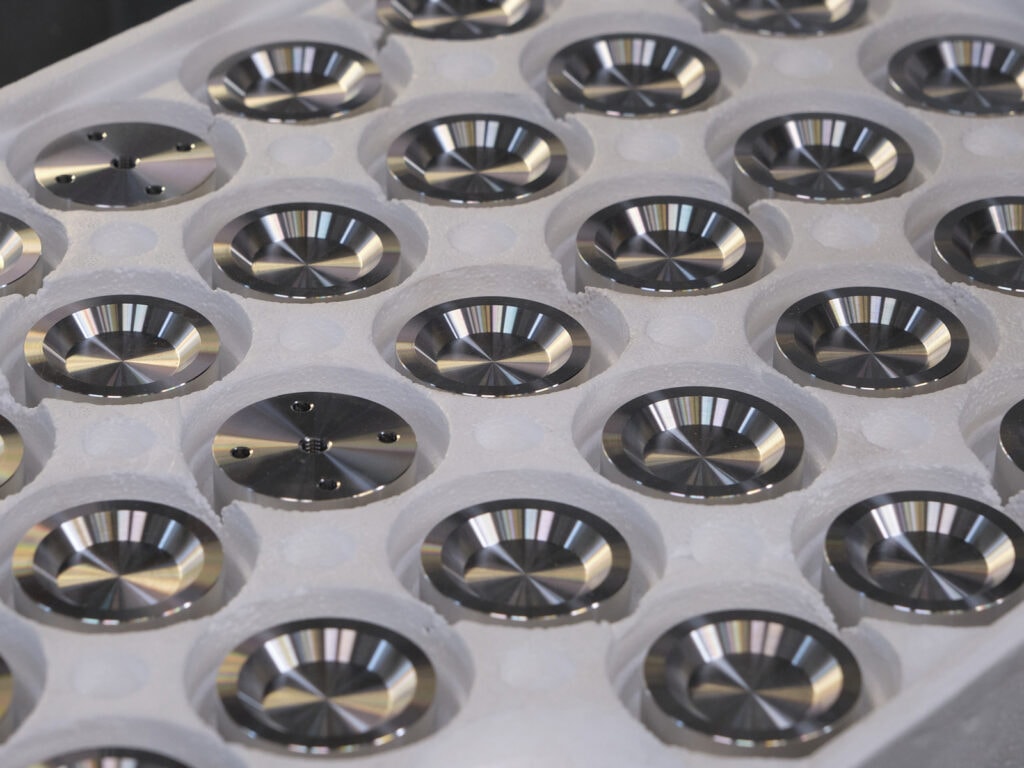
Interview with Gianluca Sigismondi and Stefano Bassan, by Elisabetta Donati De Conti
Edited by Luca A. Caizzi
EDDC: For The Instant of Change 2023, which will be housed in the spaces of Mo.1950, you decided to work on the theme of play, to therefore develop a concept that is very aggregative, inclusive and that refers to moments of sharing. How are these values important to you? How come you decided to work on this very thing at this time?
SF: This is the first time we have done a project that combines different materials produced by such different companies. Just by reasoning about this union, we decided to focus on play as an action that can distract, that makes the moment of the Salone del Mobile informal, to encourage fun, dialogue and meeting and to create the conditions for developing one’s own work. Historically, play has always encouraged dialogue that brings more people together.
EDDC: To make Tris, you have made 3D an object that is played on paper, two-dimensional. This already creates a new input, a new approach to matter and materials. How did the dialogue with the companies go? How was the process? What did you discover?
SF: We discovered many things, but not only from the material side, especially from the business and production side of materials. We realized how different the birth process is, how different the instant of change from raw material to material is between companies. At the base of this object, of this game, the part that will promote elevation is made of porcelain from Ceramiche Cesar. While visiting their production facilities, we were able to appreciate an industrial, serial, perfectly harmonious and studied approach. This approach challenged us to look for a sign that could move this seriality, that could elevate the concept of single module, slab, large tile, creating a volume composed of many small pieces. The technicalities and the change will lie in putting these different parts together to create the base of our table.
EDDC: Instead, with Rexa, how did it go?
SF: With Rexa we had a different experience, encountering a production line that is flexible and open to dialogue in order to encourage design from a more artisanal perspective. Always starting from sheet, but this time in Corian, we were able to experiment with shape, preferring a softer, more rounded line due to its technical characteristics. So we decided right away to prefer a plastic direction, thermoforming, going to create an ethereal volume, a very soft volume that plays, that contrasts the edges and unions of the porcelain stoneware at the base. The top, the last element of this table, and if you will, the one that goes to constitute the only repeated element in the object: are the checkers. Each tic-tac-toe table will have nine checkers, made in this case from QuadroDesign steel. The checkers will have a double face, one will represent the circle, the second the cross.
SF: With QuadroDesign we experimented with and introduced into the production process an additional method of creation and that is milling, which allowed us to range in lines and shapes, being able to demonstrate how such rigid, statuesque and solid objects apparently can contain within their compositions, reflections, angles and comfortable and soft spaces. The three materials then mutate into one object merging in skill and ability, playing together in a repeated series of moves that aggregate, unite and entertain. We talked about cutting, joining, thermoforming and then also gentle modifications toward softness and then milling. There are really so many different processes that meet in the same object and with even sometimes dissonant proportions. This extrusion that then meets instead the detail and the minuteness of the checkers.
EDDC: How important do you think it is in the development of the language of a contemporary object to start from or at any rate to take into account all the reasoning about innovative processing techniques and materials that are available to us also in order to overcome certain visual codes that are sometimes sedimented, but that precisely technical processing allows us to overcome?
SF: Let’s say that this concept is part of our practice as a studio. We as Finemateria leave ample space for storytelling of what are the processes related to the material, so from the production, to the sensations related to the processes and so we say that the language and the form are the result precisely of these paths that happen at the beginning of the project. The form is the result of the steps that have happened during the path with the final goal that should not be to create at any cost a new aesthetic language but to go for example to these companies that give you the opportunity to design and to put your ability into practice.